Atualmente, o torno é amplamente conhecido. A história de sua criação começa nos anos 700 dC. Os primeiros modelos foram usados para trabalhar madeira, 3 séculos depois foi criada uma máquina para trabalhar com metais.
Primeiras menções
Nos anos 700 d. C. foi criada uma unidade que se assemelha parcialmente a um torno moderno. A história do seu primeiro lançamento de sucesso começa com o processamento da madeira pelo método de rotação da peça. Nem uma única parte da instalação foi feita de metal. Portanto, a confiabilidade de tais dispositivos é bastante baixa.
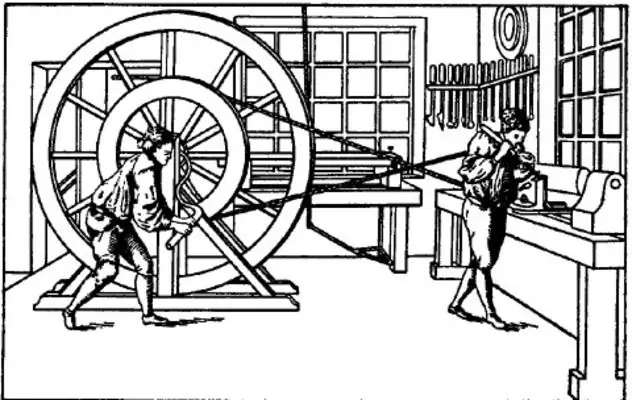
Naquela época, o torno tinha baixa eficiência. A história da produção foi restaurada de acordo com os desenhos e desenhos preservados. Para desenrolar a peça de trabalho, foram necessários 2 aprendizes fortes. A precisão dos produtos resultantes não é alta.
Informações sobre instalações, que lembram vagamente um torno, a história remonta a 650 aC. e. No entanto, essas máquinas tinham apenas o princípio de processamento em comum - o método de rotação. O resto dos nós eram primitivos. A peça de trabalho foi colocada em movimento no verdadeiro sentido da palavra. Trabalho escravo foi usado.
Os modelos criados no século 12 já tinham uma aparência de unidade e podiam obter um produto completo. No entanto, ainda não havia porta-ferramentas. Portanto, era muito cedo para falar sobre a alta precisão do produto.
O aparelho dos primeiros modelos
Um torno antigo prendeu uma peça de trabalho entre os centros. A rotação foi realizada manualmente por apenas algumas revoluções. O corte foi realizado com uma ferramenta estacionária. Um princípio de processamento semelhante está presente em modelos modernos.
Como propulsor para a rotação da peça, os artesãos utilizavam: animais, um arco com flechas amarrados com uma corda ao produto. Alguns artesãos construíram uma espécie de moinho de água para esses fins. Mas não houve melhora significativa no desempenho.
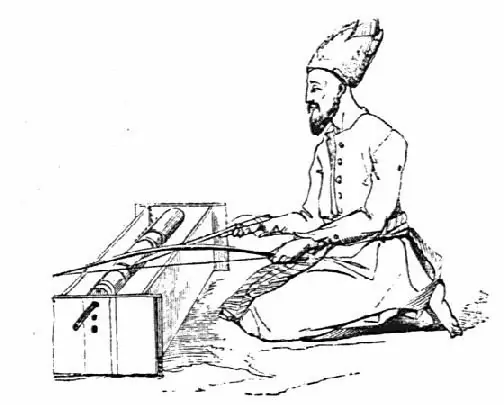
O primeiro torno tinha peças de madeira e, à medida que o número de nós aumentava, a confiabilidade do dispositivo era perdida. Os dispositivos de água rapidamente perderam sua relevância devido à complexidade do reparo. Somente no século 14 surgiu a unidade mais simples, o que simplificou muito o processo de processamento.
Atuadores precoces
Vários séculos se passaram desde a invenção do torno até a implementação do mecanismo de acionamento mais simples nele. Você pode imaginá-lo na forma de um poste fixado no meio da estrutura em cima da peça de trabalho. Uma extremidade da ochepa é amarrada com uma corda que envolve a peça de trabalho. O segundo é fixado com um pedal.
Este mecanismo funcionou com sucesso, mas não conseguiu fornecer o necessárioatuação. O princípio de operação foi construído sobre as leis da deformação elástica. Quando o pedal foi pressionado, a corda foi tensionada, o poste foi dobrado e sofreu um estresse significativo. Este último foi transferido para a peça de trabalho, colocando-a em movimento.
Tendo girado o produto 1 ou 2 voltas, a haste foi solta e dobrada novamente. Com um pedal, o mestre regulava o funcionamento constante do oche, forçando a peça a girar continuamente. Ao mesmo tempo, as mãos estavam ocupadas com a ferramenta, fazendo o processamento da madeira.
Este mecanismo mais simples foi herdado pelas seguintes versões de máquinas que já possuíam um mecanismo de manivela. As máquinas de costura mecânicas do século 20 tiveram posteriormente um design de acionamento semelhante. Nos tornos, com a ajuda de uma manivela, eles conseguiam um movimento uniforme em uma direção.
Devido ao movimento uniforme do mestre passou a receber produtos da forma cilíndrica correta. A única coisa que f altava era a rigidez dos nós: centros, porta-ferramentas, mecanismo de acionamento. Os suportes dos cortadores eram de madeira, o que os fazia torcer durante o processamento.
Mas, apesar das deficiências listadas, tornou-se possível produzir até peças esféricas. A metalurgia ainda era um processo difícil. Mesmo as ligas macias por rotação não cederam ao torneamento real.
Um desenvolvimento positivo no projeto de máquinas-ferramenta foi a introdução da versatilidade no processamento: peças de vários diâmetros e comprimentos já eram processadas em uma máquina. Isto foi conseguido por suportes e centros ajustáveis. No entanto, grandes detalhes exigiamo custo físico do assistente para implementar a rotação.
Muitos artesãos adaptaram um volante feito de ferro fundido e outros materiais pesados. O uso da força de inércia e gravidade facilitou o trabalho do manipulador. No entanto, ainda era difícil alcançar escala industrial.
Peças Metálicas
A principal tarefa dos inventores das máquinas-ferramentas era aumentar a rigidez dos nós. O início do reequipamento técnico foi o uso de centros metálicos para fixação da peça. Mais tarde, as engrenagens feitas de peças de aço já foram introduzidas.
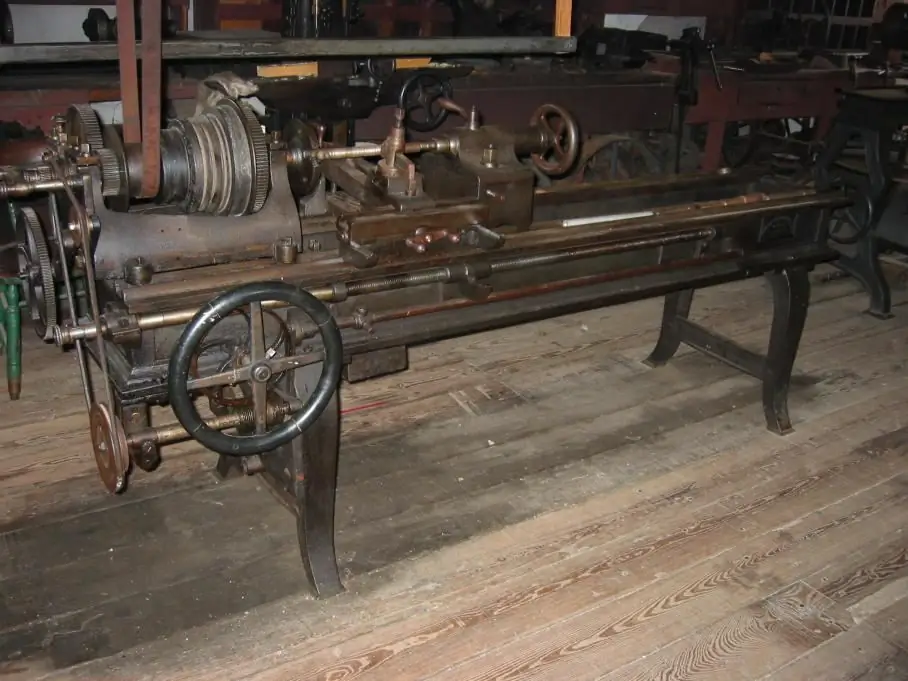
As peças metálicas possibilitaram a criação de máquinas de corte de parafusos. A rigidez já era suficiente para processar metais macios. As unidades individuais foram gradualmente melhoradas:
- suporte em branco, mais tarde chamado de unidade principal - fuso;
- paradas cônicas foram equipadas com mecanismos ajustáveis para mudar a posição ao longo do comprimento;
- trabalho no torno ficou mais fácil com a invenção do porta-ferramentas de metal, mas o escoamento constante de cavacos foi necessário para aumentar a produtividade;
- A cama de ferro fundido aumentou a rigidez da estrutura, o que possibilitou o processamento de peças de comprimento considerável.
Com a introdução de nós de metal, torna-se mais difícil desenrolar a peça de trabalho. Os inventores pensaram em criar uma unidade de pleno direito, querendo eliminar o trabalho manual humano. O sistema de transmissão ajudou a realizar o plano. O motor a vapor foi adaptado pela primeira vez para girar as peças de trabalho. Foi precedido por um motor de água.
Uniformidade do movimento do cortea ferramenta foi realizada por uma engrenagem helicoidal usando uma alça. Isso resultou em uma superfície mais limpa da peça. Blocos intercambiáveis tornaram possível realizar o trabalho universal em um torno. As estruturas mecanizadas melhoraram ao longo dos séculos. Mas até hoje, o princípio de funcionamento dos nós é baseado nas primeiras invenções.
Inventores científicos
Atualmente, na compra de um torno, as especificações técnicas são analisadas primeiro. Eles fornecem as principais possibilidades de processamento, dimensões, rigidez, velocidade de produção. Anteriormente, com a modernização dos nós, os parâmetros foram introduzidos gradativamente, segundo os quais os modelos eram comparados entre si.
A classificação das máquinas ajudou a avaliar o grau de perfeição de uma determinada máquina. Depois de analisar os dados coletados, Andrei Nartov, um inventor doméstico da época de Pedro, o Grande, atualizou os modelos anteriores. Sua ideia foi uma verdadeira máquina mecanizada que permite realizar vários tipos de processamento de corpos de rotação, cortar fios.
Uma vantagem no design de Nartov foi a capacidade de alterar a velocidade de rotação do centro móvel. Eles também forneceram blocos de engrenagens intercambiáveis. A aparência da máquina e do dispositivo lembra um torno simples moderno TV3, 4, 6. Centros de usinagem modernos têm unidades semelhantes.
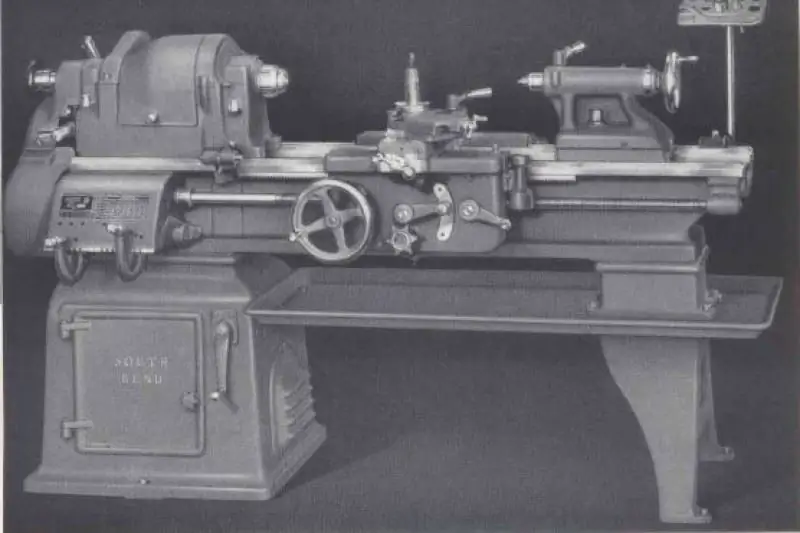
No século 18 Andrey Nartov apresentou o paquímetro autopropulsado para o mundo. O fuso transmitia o movimento uniforme da ferramenta. Henry Maudsley, inventor inglês, apresentou seuversão de um nó importante até o final do século. Em seu projeto, a mudança na velocidade de movimento dos eixos foi realizada devido ao diferente passo de rosca do fuso.
Nós Principais
Tornos são ideais para tornear peças 3D. Uma visão geral de uma máquina moderna contém os parâmetros e características dos principais componentes:
- Bed - o principal elemento carregado, a estrutura da máquina. Feito de ligas duráveis e duras, a perlita é usada principalmente.
- Suporte - uma ilha para fixação de cabeçotes rotativos ou uma ferramenta estática.
- Spindle - atua como suporte da peça. O principal nó de rotação poderoso.
- Unidades adicionais: fusos de esferas, eixos deslizantes, mecanismos de lubrificação, alimentação de refrigerante, purgadores de ar da área de trabalho, resfriadores.
Um torno moderno contém sistemas de acionamento que consistem em eletrônica de controle sofisticada e um motor, geralmente síncrono. Opções adicionais permitem remover cavacos da área de trabalho, medir a ferramenta, fornecer refrigerante sob pressão diretamente na área de corte. A mecânica da máquina é selecionada individualmente para as tarefas de produção, e o custo do equipamento também depende disso.
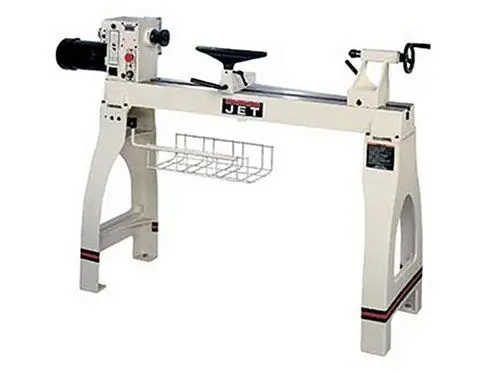
A pinça contém nós para colocação de rolamentos que são montados no fuso de esferas (par de fusos de esferas). Além disso, elementos para contato com as guias deslizantes são montados nele. A lubrificação em máquinas modernas é fornecida automaticamente, seu nível no tanque é controlado.
Nos primeiros tornos, movimentoa ferramenta foi realizada por uma pessoa, ele escolheu a direção de seu movimento. Nos modelos modernos, todas as manipulações são realizadas pelo controlador. Demorou vários séculos para a invenção de tal nó. A eletrônica expandiu bastante as capacidades de processamento.
Administração
Recentemente, tornos de metal CNC tornaram-se difundidos - com controle numérico. O controlador controla o processo de corte, monitora a posição dos eixos, calcula o movimento de acordo com os parâmetros definidos. A memória armazena várias etapas de corte, até a saída da peça acabada.
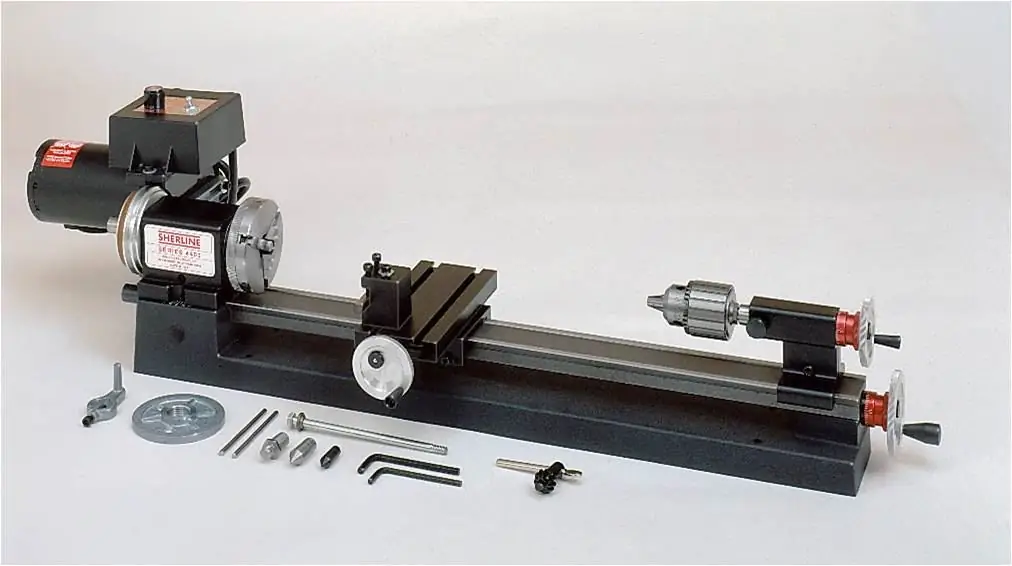
Os tornos metálicos CNC podem ter visualização do processo, o que ajuda a verificar o programa escrito antes que a ferramenta se mova. Todo o corte pode ser visto virtualmente e os erros de código podem ser corrigidos a tempo. A eletrônica moderna controla a carga do eixo. As versões mais recentes do software permitem identificar uma ferramenta quebrada.
Metodologia para controle de pastilhas quebradas no porta-ferramentas é baseada na comparação da curva de carga do eixo durante a operação normal e quando o limite de emergência é excedido. O rastreamento acontece no programa. As informações para análise são fornecidas ao controlador por um sistema de acionamento ou um sensor de potência com capacidade de digitalizar valores.
Sensores de posição
As primeiras máquinas com eletrônica tinham fins de curso com microinterruptores para controlar as posições extremas. Mais tarde, os codificadores foram instalados na hélice. Atualmente, são usadas réguas de alta precisão que podem medir alguns mícrons de folga.
Equipado com sensores circulares e eixos de rotação. O conjunto do eixo pode ser controlado. Isso é necessário para implementar as funções de fresamento que foram executadas pela ferramenta acionada. Este último era frequentemente embutido na torre.
A integridade da ferramenta é medida usando sondas eletrônicas. Eles também facilitam a localização de pontos de ancoragem para iniciar o ciclo de corte. Os apalpadores podem medir a geometria dos contornos obtidos da peça após o processamento e fazer correções automaticamente que são incluídas no re-acabamento.
O modelo moderno mais simples
O torno TV 4 é um modelo de treinamento com o mecanismo de acionamento mais simples. Todo o controle é manual.
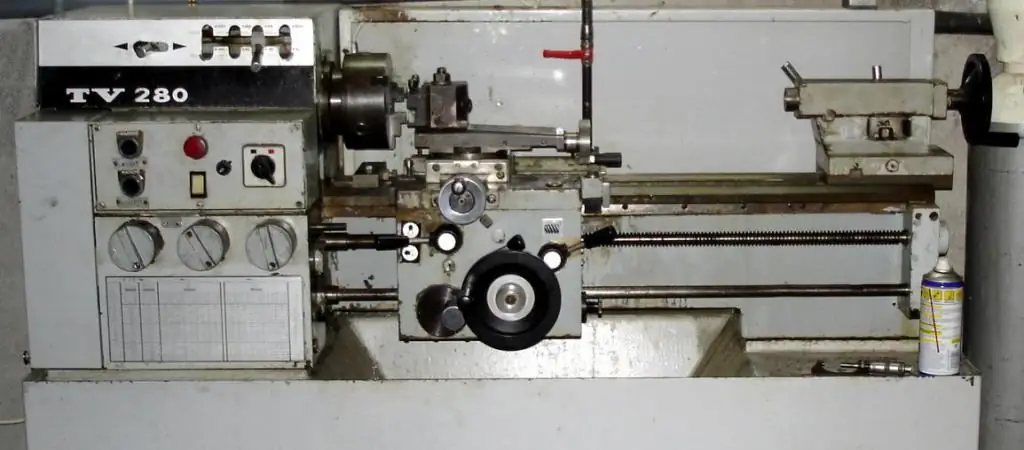
Alças:
- ajuste a posição da ferramenta em relação ao eixo de rotação;
- defina a direção da linha para a direita ou para a esquerda;
- são usados para alterar a velocidade do drive principal;
- determinar o passo da rosca;
- inclui movimento longitudinal da ferramenta;
- são responsáveis pela fixação dos nós: o cabeçote móvel e seus espinhos, cabeças com incisivos.
Flywheels movem nós:
- ponta do contra-ponto;
- carruagem longitudinal.
O projeto prevê um circuito de iluminação para a área de trabalho. Uma tela de segurança na forma de uma tela protetora protege os trabalhadores dos chips. O design da máquina é compacto, o que permite sua utilização em salas de aula, salas de atendimento.
O torno de corte de parafuso TV4 é umestruturas, onde todos os componentes necessários de uma estrutura de processamento de metal de pleno direito são fornecidos. O fuso é acionado através de uma caixa de engrenagens. A ferramenta é montada em um suporte com avanço mecânico, acionado por um par de parafusos.
Tamanhos
O fuso é acionado por um motor assíncrono. O tamanho máximo da peça pode ser em diâmetro:
- não mais que 125 mm se usinar sobre o paquímetro;
- não mais que 200 mm se a usinagem for realizada sobre a mesa.
O comprimento da peça de trabalho fixada nos centros não é superior a 350 mm. A máquina montada pesa 280 kg, a velocidade máxima do fuso é de 710 rpm. Esta velocidade de rotação é decisiva para o acabamento. A alimentação é fornecida a partir de uma rede de 220V com frequência de 50 Hz.
Recursos do modelo
A caixa de engrenagens da máquina TV4 é conectada ao motor do fuso por uma transmissão por correia em V. No fuso, a rotação é transmitida da caixa através de uma série de engrenagens. A direção de rotação da peça de trabalho é facilmente alterada pela faseamento do motor principal.
A guitarra é usada para transferir a rotação do fuso para as pinças. É possível alternar 3 taxas de alimentação. Assim, três tipos diferentes de roscas métricas são cortados. O parafuso de avanço garante um deslocamento suave e uniforme.
As alças definem o sentido de rotação do par de hélices do cabeçote. As alças também definem as taxas de alimentação. A pinça se move apenas na direção longitudinal. Os conjuntos devem ser lubrificados manualmente de acordo com os regulamentos da máquina. As engrenagens, por outro lado, retiram graxa do banho em que trabalham.
Na máquinaa capacidade de trabalhar manualmente. Volantes são usados para isso. A cremalheira e o pinhão engrenam com a cremalheira e o pinhão. Este último é aparafusado ao quadro. Este design permite, se necessário, incluir o controle manual da máquina. Um volante semelhante é usado para mover o cabeçote móvel.