O ferro é um elemento familiar a todas as pessoas do nosso planeta. E não há nada de surpreendente nisso. De fato, em termos de seu conteúdo na crosta terrestre (até 5%), esse componente é o mais comum. No entanto, apenas um quadragésimo dessas reservas pode ser encontrado em depósitos adequados para o desenvolvimento. Os principais minerais de minério de ferro são siderita, minério de ferro marrom, hematita e magnetita.
Origem do nome
Por que o ferro tem esse nome? Se considerarmos a tabela de elementos químicos, esse componente é marcado como "ferrum". É abreviado como Fe.
Segundo muitos etimologistas, a palavra "ferro" nos veio da língua proto-eslava, na qual soava como zelezo. E este nome veio do léxico dos antigos gregos. Chamavam o metal tão famoso hoje de "ferro".
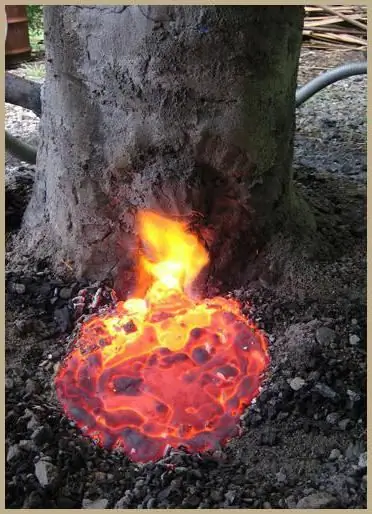
Existe outra versão. Segundo ela, o nome "ferro" nos veio do latim, ondesignificava "estrelado". A explicação para isso está no fato de que as primeiras amostras desse elemento descobertas pelo homem eram de origem meteorítica.
Uso de ferro
Na história da humanidade, houve um período em que as pessoas valorizavam mais o ferro do que o ouro. Este fato está registrado na Odisseia de Homero, que diz que os vencedores dos jogos organizados por Aquiles receberam, além do ouro, um pedaço de ferro. Este metal era essencial para quase todos os artesãos, agricultores e guerreiros. E foi a enorme necessidade dele que se tornou o melhor motor para a produção deste material, assim como o avanço técnico em sua fabricação.
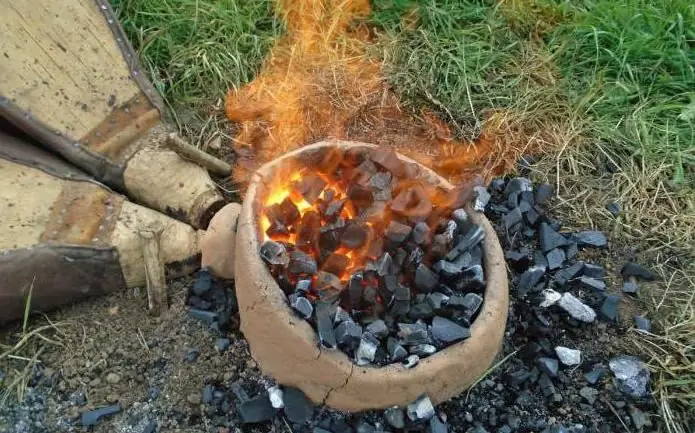
9-7 cc. BC. considerada a Idade do Ferro na história da humanidade. Durante este período, muitas tribos e povos da Ásia e da Europa começaram a desenvolver a metalurgia. No entanto, o ferro ainda está em alta demanda hoje. Afinal, ainda é o principal material utilizado para a fabricação de ferramentas.
Produto de queijo
Qual é a tecnologia de produção de ferro bloom, que a humanidade começou a extrair no início do desenvolvimento da metalurgia? O primeiro método inventado pela humanidade foi chamado de fabricação de queijo. Além disso, foi usado por 3000 anos, não mudando desde o final da Idade do Bronze até o período até o século XIII. O alto-forno não foi inventado na Europa. Este método foi chamado de bruto. Chifres para ele foram construídos de pedra ou barro. Às vezes, pedaços de escória atuavam como material para suas paredes. A última versão da forja por dentro foirevestido com argila refratária, ao qual foi adicionada areia ou chifre triturado para melhorar a qualidade.
O que faz o flash iron? Os poços preparados foram preenchidos com prado “cru” ou minério de pântano. O espaço de fusão desses fornos era preenchido com carvão, que era então completamente aquecido. No fundo do poço havia um orifício para suprimento de ar. No início, era soprado com foles manuais, que posteriormente foram substituídos por foles mecânicos.
Nas primeiras forjas, o calado natural era organizado. Foi realizado através de orifícios especiais - bicos, localizados nas paredes da parte inferior do forno. Muitas vezes, os antigos metalúrgicos forneciam o suprimento de ar através do uso de um design que permitia obter o efeito de um tubo. Eles criaram um espaço interior alto e ao mesmo tempo estreito. Muitas vezes, esses fornos foram construídos no sopé das colinas. Esses locais tiveram a maior pressão natural do vento, que foi usada para aumentar a tração.
Como resultado do processo em andamento, o minério foi convertido em metal. Ao mesmo tempo, a rocha vazia gradualmente desceu. Grãos de ferro se formaram no fundo do forno. Eles ficaram grudados um no outro, transformando-se no chamado "creep". Esta é uma massa esponjosa solta impregnada com escórias. No forno, o biscoito estava quente. Foi neste estado que eles o tiraram e rapidamente o forjaram. Pedaços de escória simplesmente caíram. Em seguida, o material resultante foi soldado em uma peça monolítica. O resultado foi um ferro chamativo. O produto final foi moldado como um pão achatado.
O que foicomposição do ferro de flor? Era uma liga de Fe e carbono, que era muito pequena no produto final (se considerarmos a porcentagem, não mais que centésimos).
No entanto, o ferro florescente que as pessoas recebiam na fornalha bruta não era muito duro e durável. É por isso que os produtos feitos desse material falharam rapidamente. Lanças, machados e facas estavam tortos e não ficaram afiados por muito tempo.
Aço
Na produção de ferro em forjas, juntamente com seus torrões macios, havia também aqueles que apresentavam maior dureza. Eram pedaços de minério que estavam em contato próximo com o carvão durante o processo de fundição. Um homem percebeu esse padrão e começou a aumentar deliberadamente a área em contato com o carvão. Isso possibilitou a cementação do ferro. O metal resultante passou a atender as necessidades dos artesãos e daqueles que usavam produtos feitos a partir dele.
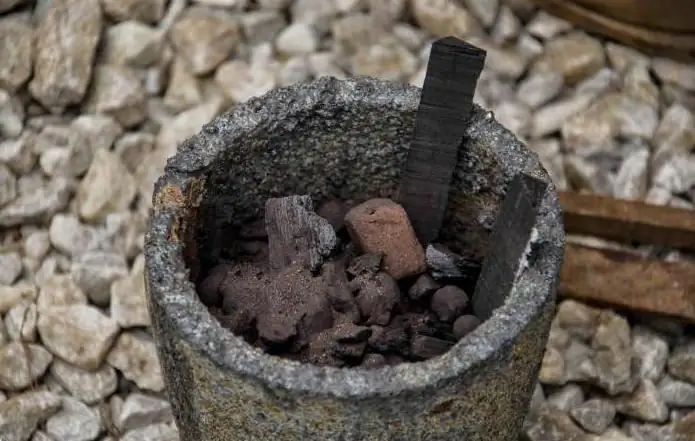
Esse material era aço. Ainda hoje é usado na fabricação de um grande número de estruturas e produtos. O aço, fundido por metalúrgicos antigos, é ferro instantâneo, que contém até 2% de carbono.
Havia também algo como aço macio. Era ferro flash, que continha menos de 0,25% de carbono. Se considerarmos a história da metalurgia, então foi o aço macio que foi produzido na fase inicial da produção de queijo. Qual é o outro nome para o ferro flash? Há também uma terceira variedade. Quando contém mais de 2% de carbono, entãoé ferro fundido.
Invenção do alto-forno
O método de floração de obtenção de ferro usando forjas de sangue bruto era altamente dependente do clima. Afinal, para tal tecnologia era importante que o vento soprasse no tubo fabricado. Foi o desejo de fugir dos caprichos do clima que levou uma pessoa a criar peles. Esses eram os dispositivos necessários para atiçar o fogo na fornalha.
Após o aparecimento do fole, as forjas para a produção de metal deixaram de ser construídas nas encostas. As pessoas começaram a usar um novo tipo de fogões, chamados "poços de lobo". Eram estruturas, uma parte das quais estava no solo, e a segunda (casas) elevava-se acima dela na forma de uma estrutura feita de pedras unidas por argila. Na base de tal fornalha havia um buraco no qual um tubo de fole era inserido para atiçar o fogo. O carvão colocado na casa foi queimado, após o que foi possível obter o cracker. Ela foi puxada para fora do buraco, que se formou após a remoção de várias pedras da parte inferior da estrutura. Em seguida, a parede foi restaurada e a fornalha foi preenchida com minério e carvão para recomeçar.

A produção de ferro brilhante tem sido constantemente aprimorada. Com o tempo, as casas começaram a ser construídas maiores. Isso exigiu um aumento na produtividade dos mechs. Como resultado, o carvão começou a queimar mais rápido, saturando o ferro com carbono.
Ferro fundido
Como é chamado o ferro flash de alto carbono? Como eramencionado acima, este é o ferro fundido que é tão comum hoje em dia. Sua característica distintiva é a capacidade de derreter em temperaturas relativamente baixas.
Tijolo de ferro - ferro fundido em forma sólida - era impossível forjar. É por isso que os antigos metalúrgicos não prestaram atenção a ele no início. De um único golpe com um martelo, esse material simplesmente se despedaçou. Nesse sentido, o ferro fundido, assim como a escória, foi inicialmente considerado um produto residual. Na Inglaterra, esse metal chegou a ser chamado de "ferro-gusa". E somente com o tempo, as pessoas perceberam que esse produto, enquanto estiver na forma líquida, pode ser derramado em moldes para obter vários produtos, por exemplo, balas de canhão. Graças a esta descoberta nos séculos 14-15. na indústria começou a construir altos-fornos para a produção de ferro-gusa. A altura de tais estruturas atingiu 3 metros ou mais. Com a ajuda deles, o ferro de fundição foi fundido para a produção não apenas de balas de canhão, mas também dos próprios canhões.
Desenvolvimento da produção de alto-forno
Uma verdadeira revolução no ramo metalúrgico ocorreu na década de 80 do século XVIII. Foi então que um dos funcionários de Demidov decidiu que, para maior eficiência na operação dos altos-fornos, o ar deveria ser fornecido a eles não por meio de um, mas por dois bicos, que deveriam estar localizados em ambos os lados da lareira. Gradualmente, o número de tais bicos cresceu. Isso possibilitou uniformizar o processo de sopro, aumentar o diâmetro da fornalha e aumentar a produtividade dos fornos.
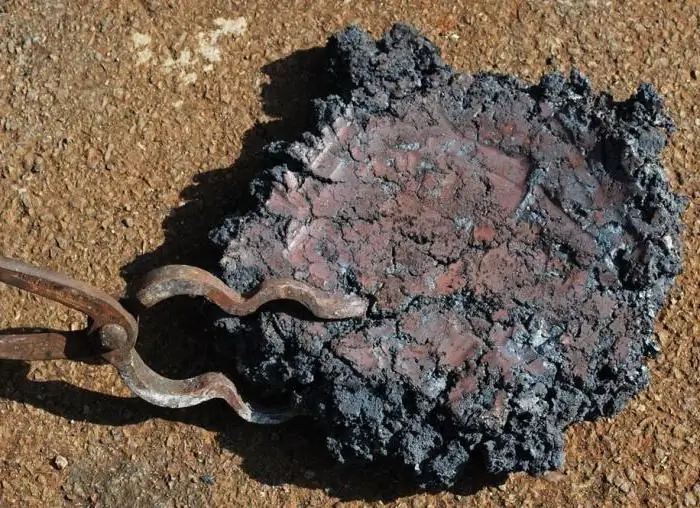
O desenvolvimento da produção de alto-forno também foi facilitado pela substituição do carvão vegetal,para o qual as florestas foram derrubadas, para coque. Em 1829, na Escócia, na fábrica de Clayde, o ar quente foi soprado pela primeira vez no alto-forno. Tal inovação aumentou significativamente a produtividade do forno e reduziu o consumo de combustível. Atualmente, o processo do alto-forno foi aprimorado com a substituição de parte do coque por gás natural, que tem um custo ainda menor.
Bulat
Qual é o nome do ferro flash, que possui propriedades únicas que foram usadas na fabricação de armas? Conhecemos este material como aço damasco. Este metal, como o aço de Damasco, é uma liga de ferro e carbono. No entanto, ao contrário de suas outras espécies, é um ferro chamativo com boas qualidades. É resistente e duro, e também capaz de produzir uma nitidez excepcional na lâmina.
Metalurgistas de muitos países tentam desvendar o segredo da produção do aço damasco há mais de um século. Foi proposto um grande número de receitas e métodos que incluíam a adição de marfim, pedras preciosas, ouro e prata ao ferro. No entanto, o segredo do aço damasco foi revelado apenas na primeira metade do século 20 pelo notável metalúrgico russo P. P. Anosov. Eles pegaram o ferro em flor, que foi colocado em uma fornalha com carvão, onde ardia uma fogueira. O metal derreteu, saturado com carbono. Naquela época, era coberto com escória de dolomita cristalina, às vezes com a adição da mais pura escama de ferro. Sob essa camada, o metal foi liberado de forma muito intensa de silício, fósforo, enxofre e oxigênio. No entanto, isso não era tudo. O aço resultante tinha que ser resfriado o máximo possívelmais lento e mais calmo. Isso possibilitou a formação, em primeiro lugar, de grandes cristais com estrutura ramificada (dendritos). Esse resfriamento ocorreu diretamente na lareira, que foi preenchida com carvão quente. Na próxima etapa, foi realizado um forjamento hábil, durante o qual a estrutura resultante não deve colapsar.
As propriedades únicas do aço damasco posteriormente encontraram uma explicação nos trabalhos de outro metalúrgico russo D. K. Chernov. Ele explicou que os dendritos são aços refratários, mas relativamente macios. O espaço entre seus "ramos" no processo de solidificação do ferro é preenchido com carbono mais saturado. Ou seja, o aço macio é cercado por aço mais duro. Isso explica as propriedades do aço damasco, contidas em sua viscosidade e ao mesmo tempo alta resistência. Esse híbrido de aço durante a fusão mantém sua estrutura de árvore, transformando-a apenas de uma linha reta em ziguezague. A peculiaridade do padrão resultante depende em grande parte da direção dos golpes, da força e da habilidade do ferreiro.
Aço Damasco
Nos tempos antigos, este metal era o mesmo aço damasco. No entanto, um pouco mais tarde, o aço Damasco começou a ser chamado de material obtido por soldagem por forja a partir de um grande número de fios ou tiras. Esses elementos eram feitos de aço. Além disso, cada um deles foi caracterizado por um teor de carbono diferente.
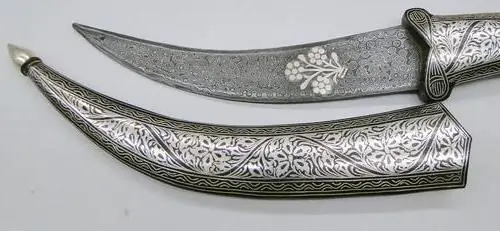
A arte de fazer tal metal atingiu seu maior desenvolvimento na Idade Média. Por exemplo, na estrutura da conhecida lâmina japonesa, os pesquisadores descobriramcerca de 4 milhões de fios de aço de espessura microscópica. Essa composição tornou o processo de fabricação de armas muito trabalhoso.
Produção em condições modernas
Os antigos metalúrgicos deixaram uma amostra de sua habilidade não apenas em armas. O exemplo mais marcante de ferro puro florido é a famosa coluna localizada perto da capital da Índia. Arqueólogos determinaram a idade deste monumento de arte metalúrgica. Descobriu-se que a coluna foi construída há mais de 1,5 mil anos. Mas o mais surpreendente está no fato de que hoje é impossível detectar até mesmo pequenos traços de corrosão em sua superfície. O material da coluna foi submetido a um exame cuidadoso. Descobriu-se que este é puro ferro flash, que contém apenas 0,28% de impurezas. Tal descoberta surpreendeu até mesmo os metalúrgicos modernos.
Com o tempo, o ferro chamativo gradualmente perdeu sua popularidade. O metal fundido em forno aberto ou alto-forno passou a ter a maior demanda. No entanto, ao aplicar esses métodos, obtém-se um produto de pureza insuficiente. É por isso que o método mais antigo de produção deste material recebeu recentemente sua segunda vida, o que permite produzir metal com as mais altas características de qualidade.
Como se chama o ferro instantâneo hoje? É familiar para nós como um metal de redução direta. Claro, o ferro em flor hoje não é produzido da mesma maneira que nos tempos antigos. Para sua produção, são utilizadas as mais modernas tecnologias. Eles possibilitam a produção de metal que praticamente não temimpurezas estranhas. Fornos tubulares rotativos são usados na produção. Esses elementos estruturais são usados para queimar vários materiais a granel usando altas temperaturas na química, cimento e muitas outras indústrias.
Como é chamado agora o ferro flash? É considerado puro e é usado na obtenção de um método que essencialmente não é muito diferente do que existia nos tempos antigos. Ainda assim, os metalúrgicos utilizam o minério de ferro, que é aquecido no processo de obtenção do produto final. No entanto, hoje as matérias-primas são inicialmente submetidas a processamento adicional. É enriquecido, criando uma espécie de concentrado.
A indústria moderna usa dois métodos. Ambos permitem que você obtenha ferro instantâneo do concentrado.
O primeiro desses métodos é baseado em trazer matérias-primas à temperatura necessária usando combustível sólido. Tal processo é muito semelhante ao realizado pelos antigos metalúrgicos. Em vez de combustível sólido, pode-se usar gás, que é uma combinação de hidrogênio e monóxido de carbono.
O que precede a obtenção deste material? Qual é o nome do ferro flash hoje? Após o aquecimento do concentrado de minério de ferro, as pelotas permanecem no forno. É a partir deles que o metal puro é posteriormente produzido.
O segundo método usado para restaurar o ferro é muito semelhante em tecnologia ao primeiro. A única diferença é que os metalúrgicos usam hidrogênio puro como combustível para aquecer o concentrado. Com este método, o ferro é obtido muito mais rapidamente. Exatamenteportanto, distingue-se por uma qualidade superior, pois no processo de interação do hidrogênio com o minério enriquecido, são obtidas apenas duas substâncias. O primeiro deles é ferro puro e o segundo é água. Pode-se supor que este método é muito popular na metalurgia moderna. No entanto, hoje é usado com pouca frequência e, via de regra, apenas para a produção de pó de ferro. Isso se explica pelo fato de ser bastante difícil obter hidrogênio puro, tanto em termos de resolução de problemas técnicos quanto por dificuldades econômicas. O armazenamento do combustível recebido também é uma tarefa difícil.
Recentemente, os cientistas desenvolveram outro, terceiro método para a produção de ferro reduzido. Trata-se da obtenção do metal a partir do concentrado de minério, sem passar pela etapa de sua transformação em pelotas. Estudos mostraram que, com esse método, o ferro puro pode ser produzido muito mais rapidamente. No entanto, este método ainda não foi implementado na indústria, pois requer mudanças tecnológicas significativas e uma mudança nos equipamentos das empresas metalúrgicas.
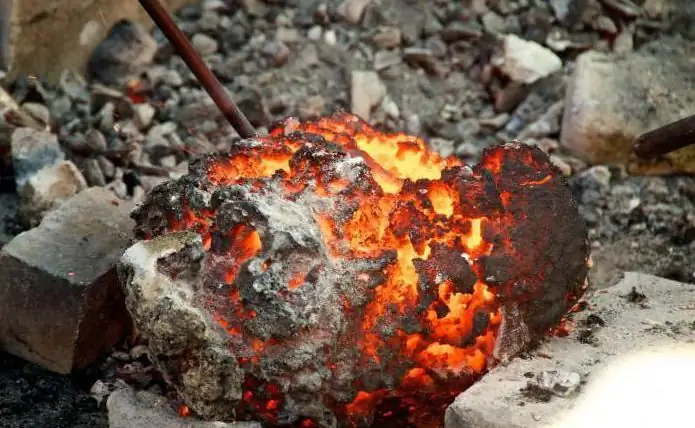
Qual é o nome do ferro flash hoje? Este material é familiar para nós como um metal de redução direta, às vezes também é chamado de esponjoso. Este é um material econômico, de alta qualidade e ecológico que não possui impurezas de fósforo e enxofre. Devido às suas características, o ferro bloomery é utilizado nas indústrias de engenharia (aviação, construção naval e instrumentação).
Fechral
Como você pode ver, hoje ao usaras tecnologias mais modernas usam materiais como ferro florescente. Fechral também é uma liga muito procurada. Além do ferro, contém componentes como cromo e alumínio. O níquel também está presente em sua estrutura, mas não mais que 0,6%.
Fechral tem boa resistência elétrica, alta dureza, funciona muito bem com cerâmicas de alta alumina, não tem tendência à corrosão e é resistente ao calor em uma atmosfera contendo enxofre e seus compostos, hidrogênio e carbono. Mas a presença de ferro na liga a torna bastante quebradiça, dificultando o processamento do material na fabricação de diversos produtos.
Fechral é usado na fabricação de elementos de aquecimento para fornos de laboratório e industriais, cuja temperatura máxima de operação é de 1400 graus. Às vezes, as peças dessa liga são usadas para outros fins. Eles são colocados em aparelhos de aquecimento doméstico, bem como em dispositivos elétricos de ação térmica. Fechral tem sido amplamente utilizado na produção de cigarros eletrônicos. Além disso, uma liga de ferro, alumínio e cromo está em demanda no campo de fabricação de elementos resistivos. Estes podem ser, por exemplo, resistores de frenagem de partida de locomotivas elétricas.
Fechral é usado para produzir arame, bem como linha e fita. Às vezes, círculos e hastes são obtidos a partir dele. Todos esses produtos são utilizados na fabricação de diversas formas de aquecedores para fornos elétricos.