Vamos falar sobre o papel do coque no processo do alto-forno. Vejamos mais de perto a essência dessa produção metalúrgica.
Hoje, o ferro e o aço são produzidos pelo processo de alto-forno, no qual o forno é um componente importante.
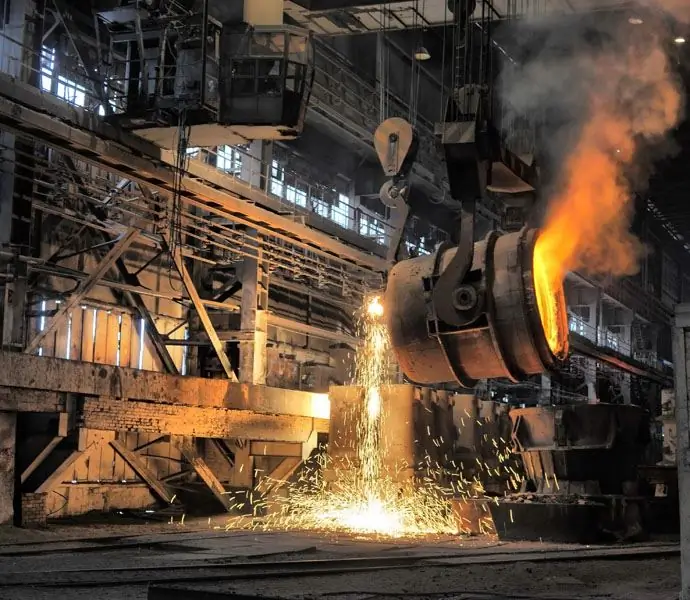
Especificações da unidade
Considere os recursos do dispositivo, sua finalidade. Os principais processos do alto-forno estão associados à fundição de coque. É um material poroso que é sinterizado a partir de uma massa de carbono obtida pela calcinação do carvão sem a presença de oxigênio atmosférico.
Um alto-forno é uma unidade poderosa e de alto desempenho, onde uma quantidade significativa de explosão e carga é consumida.
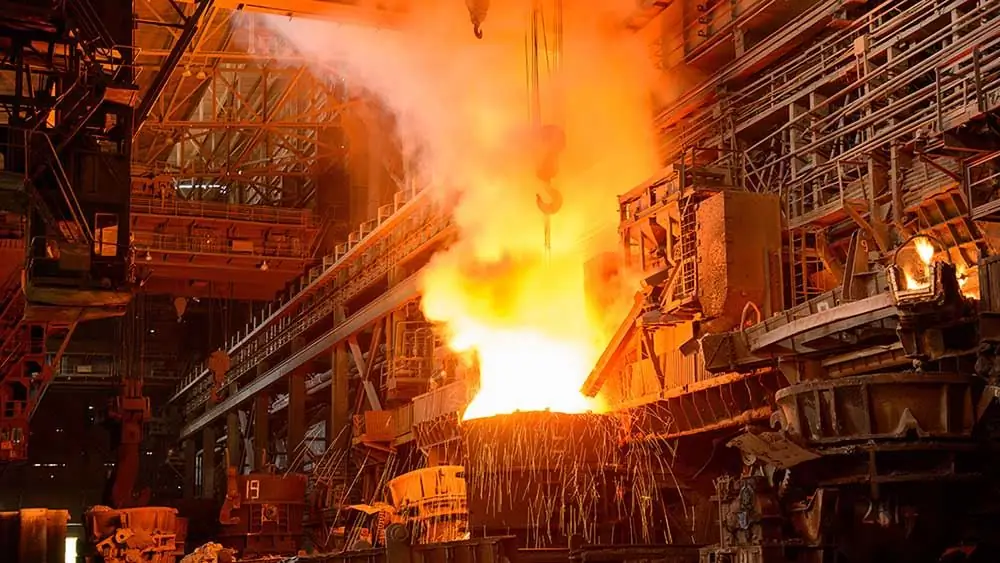
Carregando matéria prima
O alto-forno moderno requer que os materiais permaneçam nele por 4-6 horas, substâncias gasosas - 3-12 segundos. Se os gases estiverem completamente distribuídos na seção transversalfornos, você pode contar com altas taxas de fusão, a produção de ferro está em andamento. O processo de alto-forno envolve levar em conta o movimento de gases através de zonas que possuem menor resistência à carga. Portanto, quando é carregado no forno, é realizado o ajuste, a redistribuição do coque e do sinter sobre a seção transversal do forno, de modo que diferem na permeabilidade ao gás. Caso contrário, uma porcentagem maior de gases sairá do forno com uma temperatura significativa, o que afetará negativamente o uso de energia térmica, o processo do alto-forno não será totalmente eficiente.
Nas áreas de alta resistência, a mistura gasosa passará levemente aquecida, será necessário calor adicional na parte inferior do forno, como resultado, o consumo de matéria-prima aumentará significativamente.
Quais outros recursos são importantes a serem considerados ao fazer o download? O processo de alto-forno para a produção de ferro-gusa é uma produção intensiva em energia. É por isso que uma camada de aglomerado menos permeável ao gás é usada perto das paredes do forno e uma camada de coque é aumentada no centro, devido à qual o fluxo de gás é redistribuído para o centro. Os materiais são espaçados uniformemente ao redor da circunferência.
A carga é carregada em porções separadas - feeds. Uma porção é composta por vários s altos, parte de minério (aglomerado), coque. A proporção dos ingredientes originais é determinada por especialistas.
O processo de alto-forno permite a coalimentação de matérias-primas, na qual coque e sinterização são coletados em um grande cone e depois carregados em um forno.
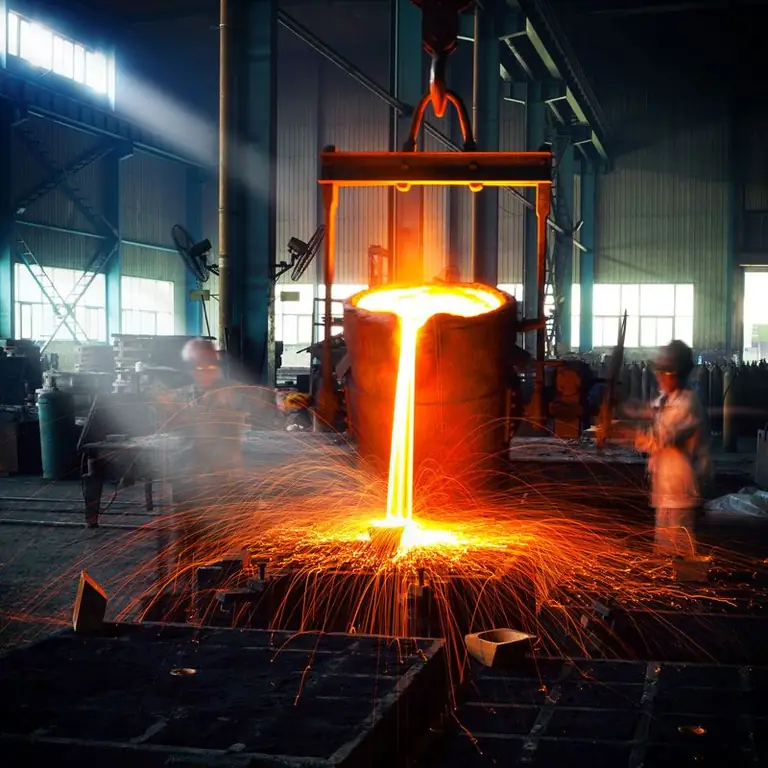
Ajuste de distribuição de lote
A distribuição de coque e aglomerado na seção transversal dos topos é controlada pelos seguintes métodos:
- alterando a ordem das matérias-primas no cone grande;
- split e split serve;
- placas móveis são instaladas perto das paredes do topo.
O processo de alto-forno envolve levar em conta certas regularidades para a introdução de materiais a granel:
- colocação de matérias-primas que caem de um cone grande em um topo com elevação - um pente;
- Na crista (no ponto de queda) da carga, os finos se acumulam, grandes pedaços rolam até o pé da crista, portanto, nesta zona, a permeabilidade ao gás da carga é maior;
- a crista é afetada pelo nível de aterro no topo, bem como a distância com um cone grande;
- o cone grande não desce completamente, então pequenos pedaços de coque chegam à periferia.
Principalmente o centro do forno recebe o material das caçambas de alimentação, que foram as últimas a serem carregadas no cone grande. Se você alterar a ordem de carregamento, poderá obter uma redistribuição de materiais na seção transversal do topo.
Para controlar o processo de distribuição da carga utilizada sobre o volume do forno, são utilizados dois aparelhos cônicos. Recentemente, alguns altos-fornos são equipados com placas móveis próximas às paredes do topo, permitindo que você altere o ângulo de inclinação, mova-as ao longo de um plano horizontal.
Peças da carga que caem sobre as placas são refletidas a partir delas, o que permite direcionar a matéria-prima para determinadas zonas do topo.
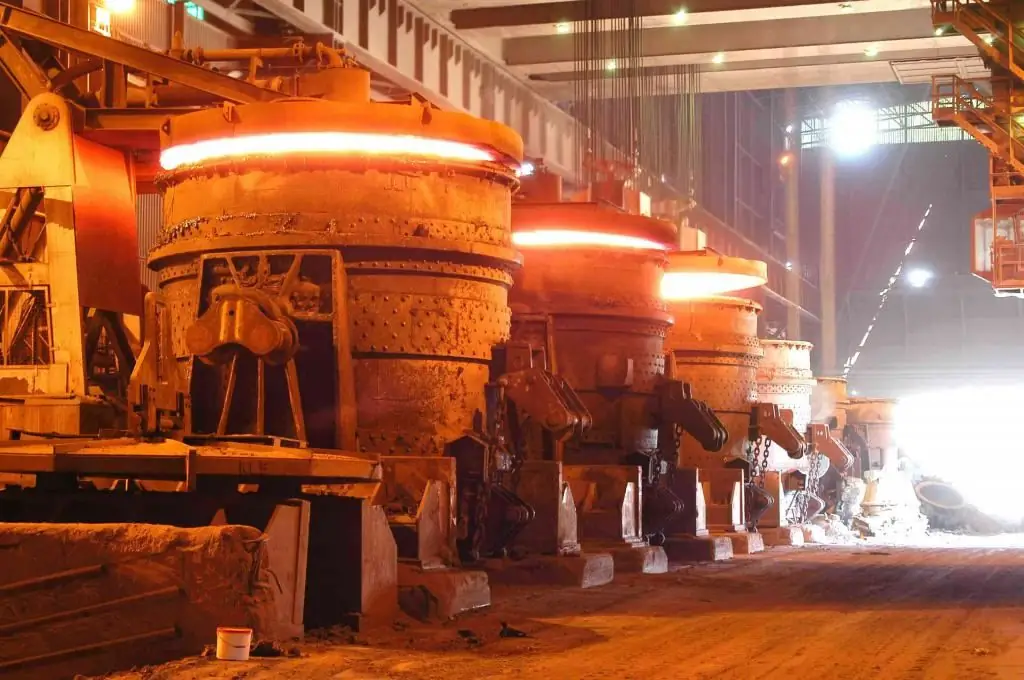
Opções de fogãosem afunilamento
Em fornos que não possuem dispositivo de carregamento cônico, o carregamento da matéria-prima é realizado através de duas moegas de eclusa que abrem alternadamente. As matérias-primas são entregues a eles por transportadores de correia inclinados, nos quais o coque e o sinter estão localizados em intervalos claros. Uma porção vem da esteira para um bunker, depois é descarregada no topo do forno ao longo de uma bandeja inclinada rotativa. Durante o período de descarga, eles fazem cerca de dez voltas completas em torno do eixo central fixo.
Ciclo de carga
É costume chamá-lo de número repetido de lotes de materiais de carga. A porção máxima é determinada pelo volume da tremonha de bloqueio do mecanismo de carregamento. O número de porções em um ciclo pode ser de 5 a 14. Como obter os produtos do processo de alto-forno na íntegra? Para responder a esta pergunta, vamos dar uma olhada na essência do processo. Com um maior teor de dióxido de carbono na mistura, a baixa temperatura contribui para a completude da troca de calor e dos processos químicos no alto-forno. Para que o aparelho funcione de forma econômica e intensiva, o teor quantitativo de dióxido de carbono ao longo do eixo e na periferia do forno deve ser reduzido e a uma altura de um ou dois metros das paredes - aumentado.
O controle de temperatura em fornos novos é feito através da introdução de sondas através de furos na carcaça. Obrigatório para todos os processos é o controle do nível de enchimento na parte superior.
Entre as inovações está o uso de métodos de medição de nível sem contato com base nas leituras de micro-ondas e sensores infravermelhos.
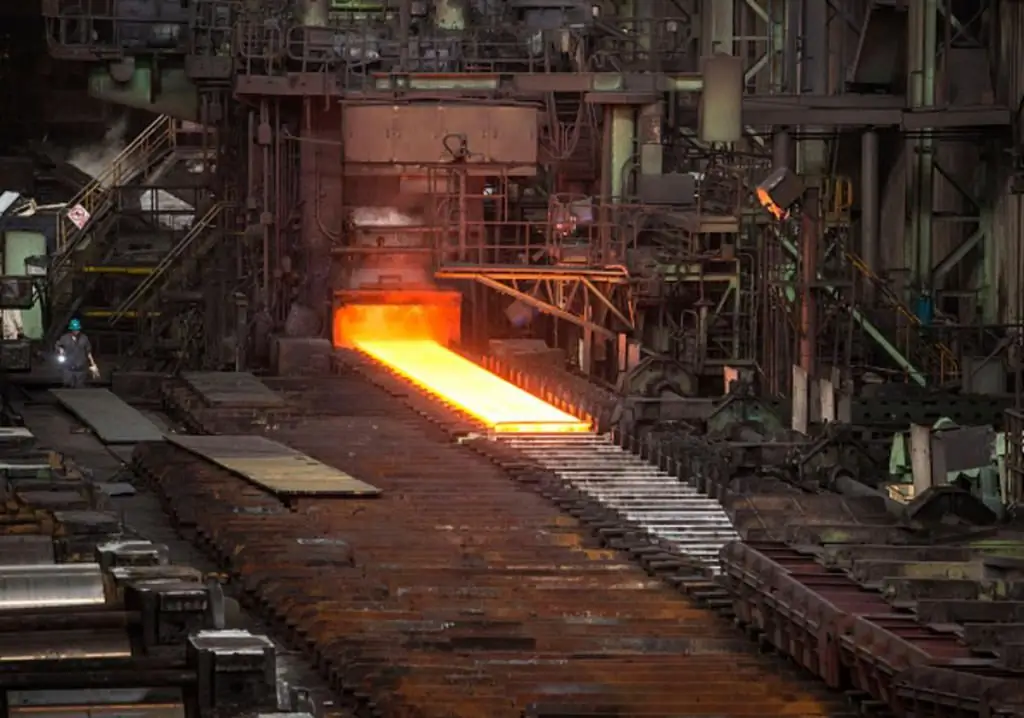
Recursos de distribuição de temperatura
Além do calor que é introduzido pelo sopro aquecido, como principal fonte de calor para o aquecimento dos gases e da carga, realizando a recuperação e compensando as perdas de calor, é possível compensar as perdas com o calor liberado durante a combustão do combustível na parte superior da lareira. À medida que os produtos gasosos se movem para cima da lareira, o calor desce para os materiais frios de carga e ocorre a troca de calor. Um processo semelhante explica a queda de temperatura de 1400 para 200 graus na saída do topo do forno.
Remova o excesso de umidade
Vamos considerar os principais processos físicos e químicos em um alto-forno. Na carga, que é carregada no alto-forno, há umidade higroscópica. Por exemplo, na composição do coque, seu conteúdo pode ser de até cinco por cento. A umidade evapora rapidamente no topo, então é necessário calor adicional para removê-la.
A umidade do hidrato aparece quando o minério de ferro marrom e o caulim são carregados no alto-forno. Para resolver o problema da produção moderna de ferro, esses minérios praticamente não são utilizados como matéria-prima.
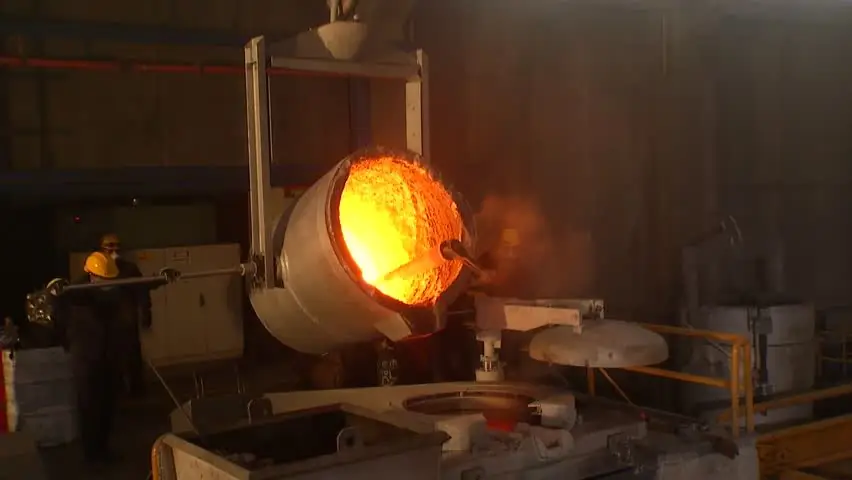
Processos de decomposição de carbonatos
Sais de ácido carbônico podem entrar no alto-forno. À medida que aquecem, se decompõem em óxidos de cálcio e carbono, e o processo é acompanhado pela liberação de uma quantidade suficiente de energia.
Recentemente, quase nenhum minério foi carregado em altos-fornos. Qual é o papel dos fundentes no processo do alto-forno? Eles aumentam sua eficáciapermitem reduzir os custos de produção. Graças ao uso de sinter fluxado, a remoção completa do calcário da carga do alto-forno pode alcançar uma economia significativa de coque. O processo de decomposição do calcário durante a aglomeração é proporcionado pela combustão de combustível de baixa qualidade.
Recuperação de Ferro
O ferro é introduzido no alto-forno na forma de óxidos. O principal objetivo do processo é maximizar a extração de ferro dos óxidos por redução. A essência do processo é remover oxigênio, carbono, monóxido de carbono, hidrogênio são usados para isso. A redução com carbono é chamada de processo direto, e a reação com substâncias gasosas é chamada de interação indireta. Quais são suas características distintivas? Na reação direta, o carbono é consumido, como resultado, sua quantidade é significativamente reduzida. O segundo tipo de redução de ferro a partir de óxidos requer uma quantidade excessiva de hidrogênio.
O processo produz ferro sólido. O grau de recuperação em ferro fundido é de 99,8%. Assim, apenas 0,2 -1% se transforma em escória.
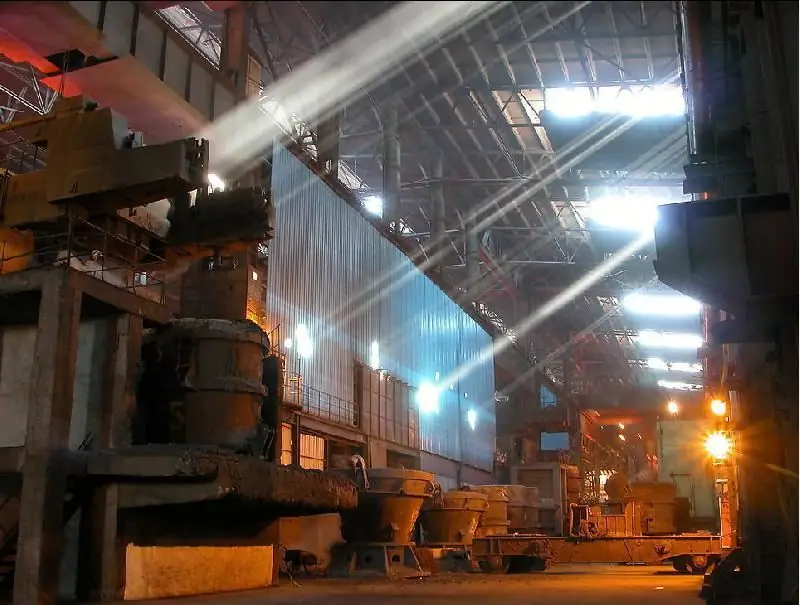
Fundição de ferro fundido manganês
No processo de fundição do ferro fundido remanufaturado, o manganês entra no alto-forno na forma de aglomerado. Em algumas quantidades, minérios de manganês na forma de silicatos de manganês contribuem para a produção de ferro fundido de manganês.
A recuperação dos óxidos de manganês ocorre em etapas. Para completar o processo, altas temperaturas devem ser ajustadas no forno. O processo de fundição de ferro gusa é acompanhado porredução de manganês apenas na proporção de 55-65%. Atualmente, devido à escassez de minérios de manganês e manganês, uma pequena quantidade de ferro fundido manganês tem sido utilizada na cadeia tecnológica. Ao mudar para ferros fundidos com baixo teor de manganês, é possível economizar não apenas o manganês propriamente dito, mas também o coque, pois seu consumo para redução direta do metal diminuirá.
Conclusão
O processo de alto-forno é um dos principais métodos de fundição de ferro e aço. Dependendo de quais componentes são introduzidos na mistura inicial, vários tipos de produto acabado são atualmente obtidos. Dentre as áreas de aplicação do ferro fundido e aço resultantes, destacamos: engenharia mecânica, indústria química, medicina, fabricação de instrumentos.